
Relevance & Importance of Quality Management Systems

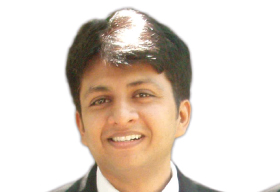
All this while from Industrial age to early 1990s India lacked emphasis on quality control due to existence of license raj. However, we started opening our doors only post liberalisation. Since then, the era of mass production of goods or industrial age type of company setup started developing gradually. In this phase, consumer begun to enjoy and focus more on the variety as compared to quality.
The 21st Century:
Global manufacturing standards began to arrive in the early 2000. This era witnessed new standards in quality, such us Six Sigma, GDP, GMP etc, which were being standardised and adopted globally including India. Soon, Indian companies realised the need to emphasize on quality in order to move up the value chain in global and domestic trade market.
In knowledge based industry such as Pharma, international standards such as GMP/GDP setup by WHO (World Health Organisation) started becoming mandatory for international trade.
Need to implement Quality standard systems:
Why do we need standards, or a quality system? With the rise of global trade in the internet era, the consumers and buyers were not restricted to just one country or region. This introduced the need to measure and standardise deliverables and timelines to ensure timely delivery of products as per specifications even from the factories set up in the remote areas of the country.
In order to demonstrate stringent quality control mechanism followed in key industries, we would like to consider an example of Pharmaceutical sector as it is the most regulated industry with globally accepted quality standards.
Example; WHO GDP standard in pharmaceuticals – India is largely known as‘Pharmacy to the World’ as it has become a hub for supplying medicines worldwide. In this global scenario, maintenance of quality becomes of utmost importance.
Hence, to ensure quality and reliability, WHO has setup a GSDP (Good storage and distribution practise) standard to monitor quality of medicine in international supply chain market.
Few key points under GSDP to ensure standardised quality in supply chain are:
• Emphasis on Environmental monitoring, i.e. Temperature control during manufacturing, storage and distribution
• Prevention of Counterfeit entry into the supply chain
• Complete pedigree (paper trail) of medicine from factory to patient
• Ability to recall any batch of medicine in case of sub standard quality detection
• Pharmacovigilance and Adverse drug reaction monitoring
• Track and trace of medicines from Factory to patient using 2D barcoding
Pharma industry lays an excellent example of importance of quality standards and it’s relation to global business. This is due to the fact that without quality certifications in place a pharma company is unable to sell medicines internationally; hence the industry had to adopt standards at an early stage as it became a matter of survival.
Getting Certified: Preparing for Certification
There are several steps involved to get certified:
• Qualitative measures cannot be implemented in one day. It is a continuous and a long term process to attain the desired quality.
• The business processes need to streamlined.
• Clearly defined Job responsibilities of each team member along with regular professional training.
• Each member needs to understand his / her role and the consequence of negligence.
• SOPs (Standard operating procedures): A clearly written and simple to understand SOPs are the foundation of any quality systems. Unfortunately, SOPs are never written in simple and easy to understand language - this is the ‘Achilles heel’ of quality management worldwide).
• Preparation of SOPs: The right approach to prepare SOPs is by interacting with team members who will actually do that particular task and then convert the same into the SOP that can be followed to meet the Quality management systems.
• Regular internal audits: An internal check is a must to ensure quality and reduce possibility of mistakes. An internal audit is extremely significant, however almost every company follow a system of conducting an external audit before the internal, only to realise that simple mistakes can jeopardise the quality certification.
• Training program and training calendar: Regular, planned training is the single most important factor in any Quality management system.
• Pro Active not Re Active: QMS is about shifting the mind sets from RE Active to proactive. Quality management is about an ability to identify issues before they cause a problem like substandard product disrupting a supply chain.
• Selection of appropriate certification body for accreditation: Lastly, choosing the right certification body to get the company accredited/certified becomes essential First step in this is the identification of destination market or target audience. And then comes in play the selection of a certification body whose certification is approved/recognised by the government of the destination market.
Quality management and certification gives an organisation or a product a clearly defined and measurable ‘Attribute’. In the era of globalization, where trade is done through internet, without seeing each other, a Quality certificate is the only edge one can have over their competitors.
Few key points under GSDP to ensure standardised quality in supply chain are:
• Emphasis on Environmental monitoring, i.e. Temperature control during manufacturing, storage and distribution
• Prevention of Counterfeit entry into the supply chain
• Complete pedigree (paper trail) of medicine from factory to patient
• Ability to recall any batch of medicine in case of sub standard quality detection
• Pharmacovigilance and Adverse drug reaction monitoring
• Track and trace of medicines from Factory to patient using 2D barcoding
A clearly written and simple to understand SOPs are the foundation of any quality systems
Pharma industry lays an excellent example of importance of quality standards and it’s relation to global business. This is due to the fact that without quality certifications in place a pharma company is unable to sell medicines internationally; hence the industry had to adopt standards at an early stage as it became a matter of survival.
Getting Certified: Preparing for Certification
There are several steps involved to get certified:
• Qualitative measures cannot be implemented in one day. It is a continuous and a long term process to attain the desired quality.
• The business processes need to streamlined.
• Clearly defined Job responsibilities of each team member along with regular professional training.
• Each member needs to understand his / her role and the consequence of negligence.
• SOPs (Standard operating procedures): A clearly written and simple to understand SOPs are the foundation of any quality systems. Unfortunately, SOPs are never written in simple and easy to understand language - this is the ‘Achilles heel’ of quality management worldwide).
• Preparation of SOPs: The right approach to prepare SOPs is by interacting with team members who will actually do that particular task and then convert the same into the SOP that can be followed to meet the Quality management systems.
• Regular internal audits: An internal check is a must to ensure quality and reduce possibility of mistakes. An internal audit is extremely significant, however almost every company follow a system of conducting an external audit before the internal, only to realise that simple mistakes can jeopardise the quality certification.
• Training program and training calendar: Regular, planned training is the single most important factor in any Quality management system.
• Pro Active not Re Active: QMS is about shifting the mind sets from RE Active to proactive. Quality management is about an ability to identify issues before they cause a problem like substandard product disrupting a supply chain.
• Selection of appropriate certification body for accreditation: Lastly, choosing the right certification body to get the company accredited/certified becomes essential First step in this is the identification of destination market or target audience. And then comes in play the selection of a certification body whose certification is approved/recognised by the government of the destination market.
Quality management and certification gives an organisation or a product a clearly defined and measurable ‘Attribute’. In the era of globalization, where trade is done through internet, without seeing each other, a Quality certificate is the only edge one can have over their competitors.